NorthWestern Energy’s Natural Gas Emissions Reduction Plan
NorthWestern Energy is committing to net zero carbon by 2050, which also includes our plan to reduce methane emissions by 30% by 2030 and ultimately eliminate all methane emissions by 2050.
At NorthWestern Energy, we’ve already avoided or reduced methane emissions from our natural gas distribution, transmission, and storage systems over the past decade by maintaining our plastic and cathodically protected steel distribution lines, embarking on a storage well inspection program, and installing Excess Flow Valves on our distribution system. Additionally, NorthWestern Energy has modernized the design of compressor stations to minimize the blowdown of compressor piping during testing and activation of emergency shut down system. We have also modernized the design of many of our city gate stations to include low bleed or, in many cases, no bleed regulating systems as well as using monitor regulator systems to avoid blowing gas into the atmosphere with relief valves in the event of a failure.
This report outlines the path to further emissions reductions by:
- Accelerating the leak survey program.
- Rehabilitating or retiring older infrastructure.
- Embracing new technologies and operational practices to keep gas flowing more safely and efficiently than ever.
- Energy efficiency efforts.
We expect these measures — detailed below — will reduce methane emissions by 30% by 2030.
From 2030 to 2050, we will continue to optimize the steps noted above and will invest in new technologies that will help us further reduce emissions. As an example, we are now partnering with RNG producers who are using new technology to capture and use methane that would otherwise be emitted into the atmosphere.*
*Note: NorthWestern Energy revised this paragraph on Feb. 17, 2025.
By achieving our 30% reduction goal, we’ll reduce our methane emissions by more than 4,000 metric tons — that’s the equivalent of removing about 22,000 vehicles from the road for a year or preserving more than 122,000 acres of forest.
Our natural gas system
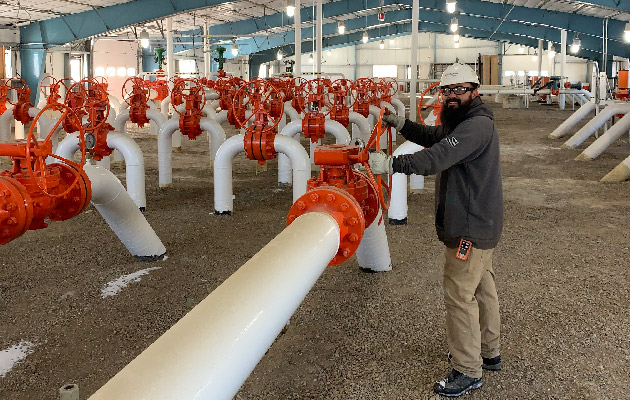
Our natural gas system
system is made up of 2,384 miles of cathodically protected coated steel lines and 4,994 miles of plastic line. We do not have any bare steel or cast iron pipelines on our system, which historically have been associated with high leak rates. We move more than 40 billion cubic feet (Bcf) of natural gas through our transmission system annually.
Compressor stations move natural gas through our interstate transmission pipeline system, to and from our underground storage fields and to city gate stations, where odor is added and pressure is regulated for safe delivery to homes and businesses.
We own and operate 10 transmission, 4 storage, and 8 production compressor stations and 3 underground gas storage fields with a total storage capacity of 17.85 Bcf. We also receive supply from interstate and third‑party pipeline sources. Compressor stations inject gas into storage fields during the summer when we can purchase gas at lower cost, transport gas through the system and withdraw gas from storage fields to increase system supply during the winter when demand is highest, and allow us to achieve system supply and demand balancing.
Methane as a greenhouse gas
Methane emissions from natural gas systems
Producing, processing, storing, transmitting, and distributing natural gas can result in two types of methane emissions:
- vented gas
- fugitive emissions.
Gas sometimes is intentionally vented to create safe working conditions for maintenance and repair, or as part of emergency testing procedures. Vented gas is typically tracked and associated with specific events or locations.
By contrast, fugitive emissions are distributed across the gas system and are usually associated with minute leaks along low‑pressure pipe, fittings, or valves that do not pose a public safety risk. Fugitive emissions are mitigated through robust system maintenance processes, leak survey, and repair and the replacement of older, vintage materials, and equipment.
The EPA requires owners of natural gas transmission, storage, and distribution systems to report emissions of methane and other GHGs from some sources annually if the emissions exceed a threshold. Gas system owners also can participate in voluntary reporting programs designed to reduce methane emissions.
Voluntary Commitments
We joined the EPA Methane Challenge program and are committed to using best management practices to further reduce fugitive methane emissions. The Methane Challenge is a voluntary program. Participants transparently report systematic and comprehensive actions to reduce methane emissions and are recognized as leaders in reducing methane emissions in the U.S. Reducing methane emissions reduces operational risk, increases efficiency, and demonstrates company concern for the environment, with benefits spanning from climate change to air quality improvements to conservation of a non‑renewable energy resource. Methane Challenge partners also enjoy the benefits of the Natural Gas STAR Program such as information sharing, technology transfer, peer networking, voluntary annual reporting, and communication of achievements.
Our Montana operations meet the reporting threshold of the Environmental Protection Agency’s Greenhouse Gas Reporting Program, however, we also report greenhouse gas emissions from our South Dakota and Nebraska distribution systems, including methane, under the EPA’s GHGRP even though only our Montana operations meet the reporting threshold. In addition to GHG reporting, we voluntarily disclose emissions metrics developed by the American Gas Association (AGA) and the Edison Electric Institute (EEI). The AGA‑EEI partnership, led by a CEO taskforce, established the Natural Gas Sustainability Initiative (NGSI), which is in the process of developing additional metrics beyond those required by mandatory reporting.
What we're doing now
Enhanced Infrastructure Replacement Program
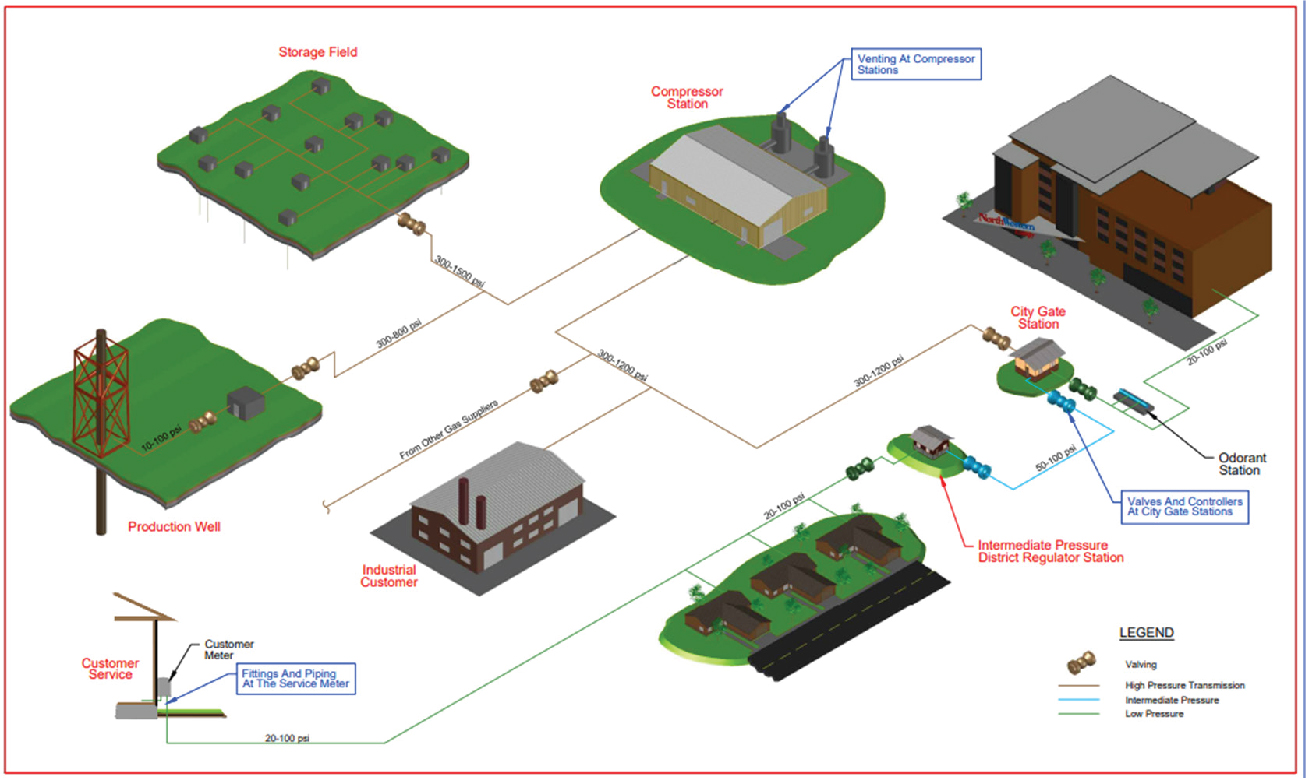
Enhanced Infrastructure Replacement Program
NorthWestern Energy began “covering” mechanical couplings on older pipelines decades ago to improve cathodic protection on our pipelines as well as minimize the risk of venting natural gas at these couplings. Additionally, we are replacing sections of these lines to improve the reliability and safety of the lines.
Our city gate replacement and farm tap conversion program converts large farm taps to city gate stations to improve the reliability of service to the customer and replaces older equipment with more modern equipment that is less likely to vent. Our city gate replacement program also replaces aging infrastructure with modern control systems designed for low or no bleed pressure regulation. We also incorporate monitor regulators to minimize the risk of blowing methane into the atmosphere while maintaining safe, reliable service to our customers.
Our compressor modernization program includes using best available control technology on older compressors. This technology improves the emissions from the units as well as reducing the time and effort to bring units on line when they are needed to meet load demands.
Additionally, we recently started the in‑line inspection of our existing pipelines. Many of these lines are in high or moderate consequence areas. Modern technology allows for a thorough inspection of lines, again minimizing the risk of venting gas as well as improving the safety and reliability of the gas transmission system.
Gas Distribution Infrastructure Program (GDIP)
Annual Leak Survey – Distribution System
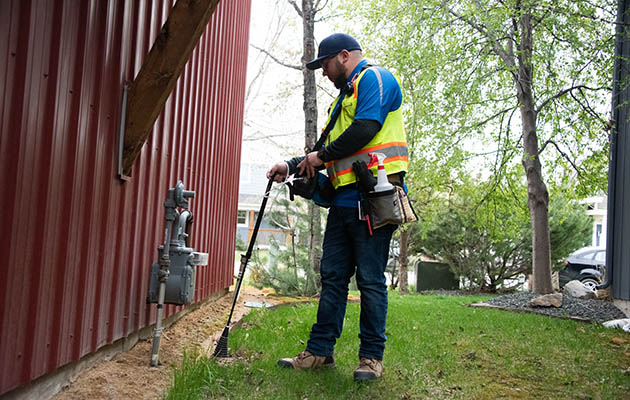
Annual Leak Survey – Distribution System
Damage Prevention Program
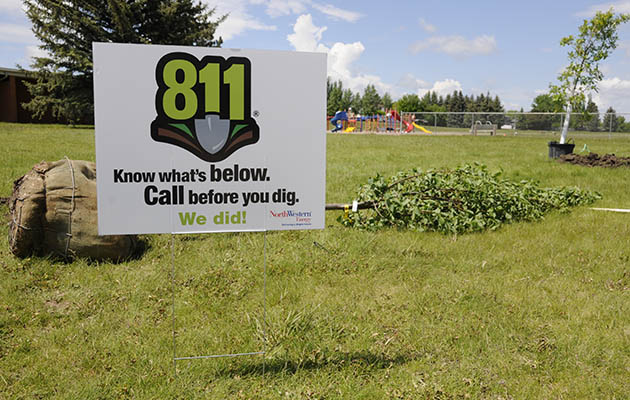
Damage Prevention Program
We work to reduce damage incidents and associated emissions by participating in the Call Before You Dig / 811 system. We also have public safety employees who participate in contractor safety fairs and develop information for contractors on safe digging practices and the dangers associated with excavating near natural gas infrastructure. Similarly, our public safety program promotes safe digging practices for the public. This program, among other things, educates homeowners on the need to call 811 at least three days prior to any digging.
Our gas transmission system has a third‑party process in Montana and South Dakota that includes a standby requirement and process. Standbys are completed on all crossings and parallel digs that will be in close proximity of the transmission lines. Anyone that submits a locate request that is in the vicinity of a transmission line is contacted to discuss work that is planned. This same process takes place with excavations near our production and gathering system.
Storage Well Integrity Inspection Program
In 2018, we implemented an Underground Storage Integrity Management Plan (UGSIM). Part of the UGSIM is an 8‑year effort to inspect each underground natural gas storage well, increasing overall well integrity and performance. We assess all storage wells for overall integrity, in addition to other safety, environmental and performance standards. Equipment is updated at this time to improve overall integrity and reliability. To date we have replaced leaking wellheads, valves, and fittings. We are also installing additional monitoring and implementing procedures to create a culture of proactive leak detection at our storage wells. After the initial baseline inspection period the UGSIM will continue on and storage wells will be continuously evaluated and inspected using a risk model. The risk model will drive which wells are inspected and how often based on data we gather as the program progresses.
Well Abandonment Program
Since 2015 NorthWestern Energy has plugged 57 non‑producing wells, initially on a reactive as‑needed basis or if funds were available. Beginning in 2019 a dedicated program was created to plug approximately 10 wells per year. The process of plugging a well removes all above‑grade equipment such as valves and flanges that may contribute to fugitive emissions. We will continue plugging at least 10 wells each year.
Production Artificial Lift
Artificial lift systems such as pumping units, velocity strings, and plunger lifts are installed on candidate wells to alleviate the need to blow wells to atmosphere to remove liquids that accumulate in the natural gas well bores. The installation of the artificial lift systems can drastically reduce the amount of gas that is blown to atmosphere. The artificial lift systems also are able to extend the life of the well. Artificial lift installations are anticipated to be part of the ongoing operations for the life of the fields.
Liquid Removal
At our storage wells we are reducing the need for natural gas emissions associated with liquids removal from the wellbores and from the liquid traps associated with the pipeline gathering system. We are evaluating the critical flow rates in our storage wells that will keep liquids unloaded out of the well and in a separation vessel at the service, reducing the need to blow wells to atmosphere to clean out fluid accumulation in the wellbore. Automation at the separation vessels will eliminate the need to blow water out of the pipelines and separation vessels with methane. We are evaluating improved systems for handling water production at the wellhead. By removing the water as soon as possible we can reduce our need to use natural gas to blow the fluids out of the pipeline. One of our wells has automation installed and its effectiveness is being evaluated to establish the best operating procedure. After a process is proven and determined to be good practice, the automation on the separation vessels could be introduced companywide with 20‑30 installations completed each year until all storage well separation vessels are upgraded.
Temporary Compression on Transmission Pipeline
For employee and public safety, we must lower pressure and remove natural gas from a high‑pressure transmission pipeline before performing maintenance and other work. Historically, we reduce the pipeline’s pressure as much as possible by rerouting the gas into neighboring pipelines, then vent the remainder of the gas to create a safe working condition. The venting practice, while standard in the industry, results in methane emissions and wastes valuable natural gas. That’s why over the past decade we’ve implemented procedures to drawdown pipelines using city gates or compressor stations. In 2022, we plan to implement temporary compression to further reduce the pressure in our pipeline during maintenance activities. The drawdown procedures and use of temporary compressor technology allows us to transfer more natural gas to adjacent pipelines and significantly reduces the volume vented to the atmosphere or flared when appropriate. We also proactively replace transmission pipelines to reduce the number of repair projects and lower the likelihood of venting. We are committed to using drawdown procedures and/or temporary compression as well as flaring for planned transmission projects. These actions will reduce methane emissions.
Impact of Current Programs and Practices
Our plans for the Future
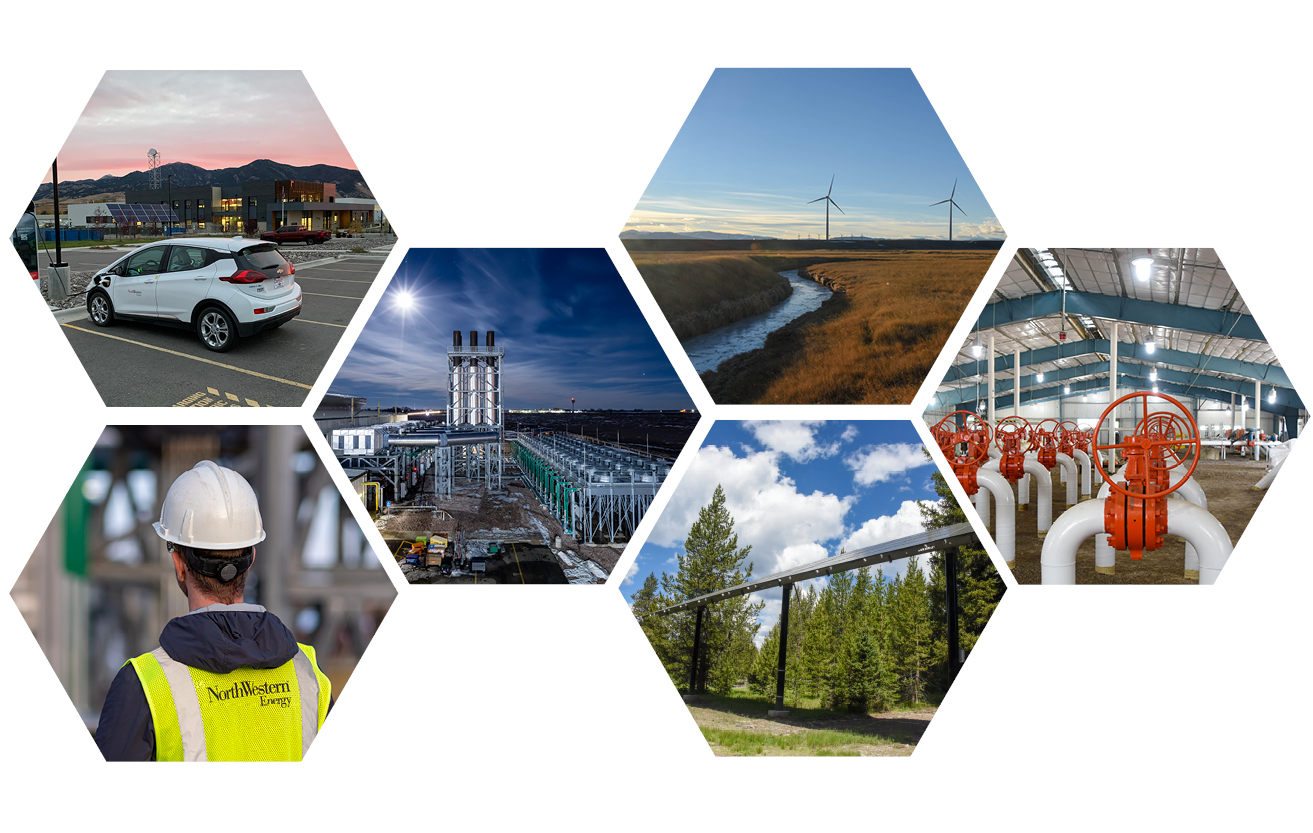
Our plans for the Future
Accelerated Leak Reduction Program
Natural gas pipelines, especially those at lower pressure such as distribution pipelines, can leak gas and thus contribute to emissions. Our leak detection program tracks leak repair as required by federal regulations. We are currently exceeding federal and state survey requirements and are looking to improve upon this even more.
Asset Retirements/Replacements
As part of our long term strategy that includes compliance with federal regulations, we will continue to evaluate all natural gas assets for effectiveness in operations as well as for their impact on the environment. For example, our maximum allowable operating pressure, MAOP, reconfirmation program is slated to spend approximately $15 million per year through 2035 to replace assets that will no longer meet the recently enacted, more stringent requirements of federal regulations. This program is intended to improve the safety and reliability of the gas system, but also has the benefit of reducing methane emissions as well as the risk for a substantial methane release.
We are also expanding a program in place for decades to replace obsolete control valves at metering and regulating stations throughout our service territory. This program extends into natural gas compression as well. An example is the removal of obsolete and underutilized gas compressors at our Telstad facility in 2015. NorthWestern removed a number of compressor units as well as the associated piping from this facility, thus reducing emissions and the potential for significant emissions. Many of the compressor units removed at this facility were installed in the 1950s. Another example was the removal of the original compressor units at our Absarokee Compressor facility and the replacement of these units in 2018 with modern compressors and new yard piping within the facility. Lastly, we currently have a program in our Dry Creek Storage facility to replace old gathering pipelines as well as valve assemblies and continue to evaluate the effectiveness of our existing compression at this facility.
Compressor Engine Rod Packing
Compressor station engines help pull gas from storage fields and push the gas through our system. Each compressor engine and associated cylinders are fitted with piston rods and required “packing systems” that maintain a seal around the piston rod to prevent high‑pressure gas from leaking. Even in new condition, however, packing systems have some small leaks. As these systems age and engine alignment changes, more leaks tend to occur.
We will continue to evaluate how best to align rod replacement schedules with packing replacements to reduce emissions. We will use emission monitoring equipment to quantify and reduce emissions associated with compressor stations.
Compressor Station Emergency Testing
We conduct annual tests of the fire gate systems at our compressor stations which simulate the venting of natural gas from a compressor station upon detection of an ignition source. Fire gate testing causes methane to be released to the atmosphere. We will evaluate the best management practice of installing block valves that function as a bypass system. This could significantly reduce emissions to the atmosphere during testing. We will evaluate which compressor station sites are best suited for the technical feasibility of similar technologies.
Compressor Station Air Starters
Currently, natural gas is used to start our compressor engines, however, we will evaluate the possibility of using air instead. This involves installing large air compressors, dryers, and volume tanks along with some infrastructure modifications and changes.
Distribution System Leak Survey and Maintenance Alignment
We survey for leaks at our city gates and are looking to enhance our accelerated leak survey program. In addition, when sites are rebuilt or upgraded, upgraded equipment such as EFVs, and low bleed or no bleed pneumatic devices are installed, which can reduce fugitive emissions at these sites. While emissions from these systems are a small portion of our overall emissions, simple procedural changes and alignment can efficiently reduce methane emissions. We are looking to begin aligning leak surveys and findings with upgrade and maintenance schedules to prioritize sites with higher emission levels. This alignment is expected to lower emissions for these assets over the long term.
Renewable Natural Gas
NorthWestern Energy supports the development of innovative energy sources to reduce emissions, such as Renewable Natural Gas (RNG) facilities that capture methane and put it to productive use rather than allowing it to be released into the environment.
In South Dakota, NorthWestern Energy currently accepts pipeline-quality gas from RNG facilities. This gas is produced from biogenic sources, specifically livestock waste from local agricultural operations using RNG facilities such as anaerobic digesters.
In the future, NorthWestern Energy plans to accept pipeline-quality gas from RNG facilities in Montana and Nebraska. These facilities may use a variety of biogenic sources, putting to productive use methane generated at municipal wastewater facilities, landfills, and agricultural operations.
While NorthWestern Energy accepts pipeline-quality gas from RNG facilities, the company currently does not purchase the environmental attributes associated with the gas. The company delivers “brown gas” (i.e., the molecules of gas without the environmental attributes) to customers.*
*Note: NorthWestern Energy revised this paragraph on Feb. 7, 2025.
Future Technology Evaluation
Future technologies may provide more opportunities to reduce methane emissions and allow us to measure our total system emissions more accurately. Currently, we use EPA emission factors to estimate our emissions but are looking towards new and proven technologies to directly measure methane emissions. We will also evaluate whether we can apply new technologies to our natural gas delivery system in the area of leak surveys, equipment, and work procedures.
Net Zero Goal
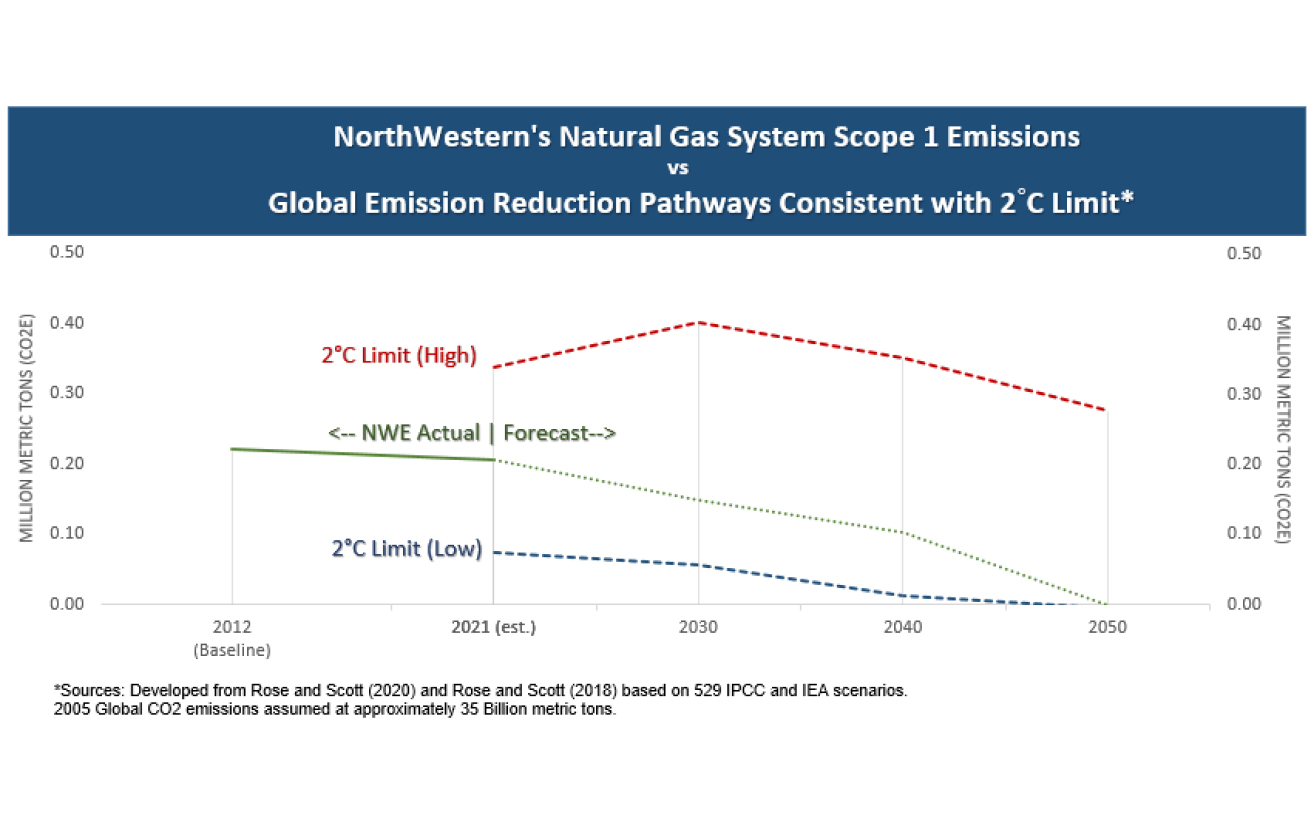
Net Zero Goal
NorthWestern Energy is committed to emission reductions across our operations and is setting the ambitious target of a net zero methane emission gas delivery system by 2050. To accomplish this goal, we plan to reduce methane emissions from our natural gas delivery system by 30 percent by 2030 from 2020 levels.
This goal builds on reductions achieved through existing programs. Meeting the challenge of a 30 percent methane emissions reduction will require commitment to new practices, exceptional performance, and innovative solutions. It will also require policy and regulated support.
To reach Net Zero by 2050, we will continue improving our operations with advanced technologies not widely available today and will explore using cleaner fuels such as RNG to further clean our gas supply. In addition, if any emissions remain after these efforts we will deploy carbon credits as an offset to achieve net zero.